Bringing a Processor’s Work Full Circle with Digital Recordkeeping
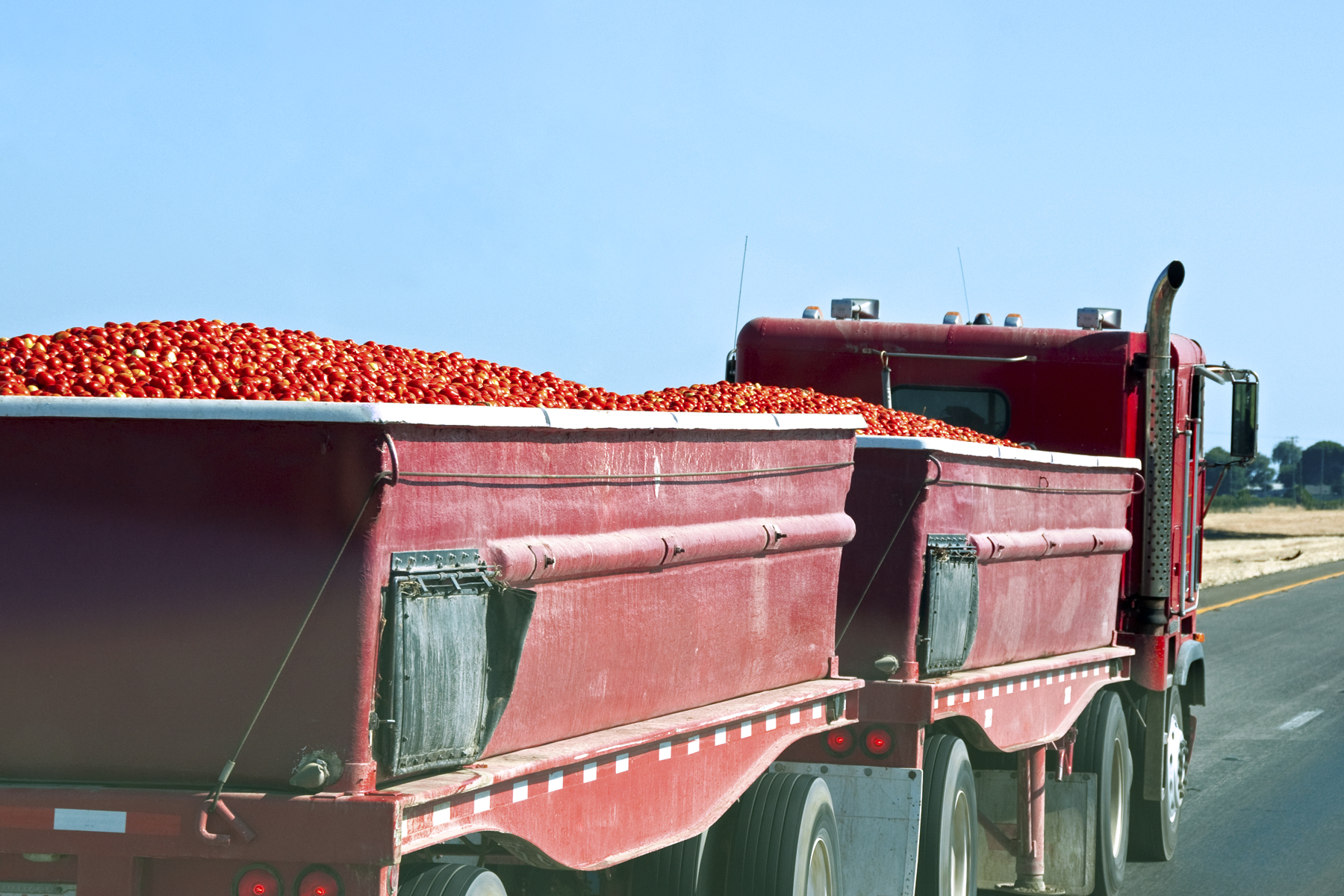
In recent history, paper records were the only option for food processors. Pre-printed pesticide reports were filled out and delivered to processors manually. Employees in the processor’s pesticide reporting program cataloged and processed each report, hoping it was filled out with a pen instead of smudged pencil. The process was time consuming and required a large temporary workforce to complete. When audits came along, weeks were devoted to putting together all of the data required.
Fifteen years ago, when Renee Rianda started working as the pesticide and sustainability manager at Morning Star, this was the processor’s reality. In the early years with the company, Rianda spent almost all of her time printing and compiling reports on pesticide use. The industry was on the cusp of switching to digital records, but fear of that type of change threatened to eliminate the option of storing this data virtually instead of on paper.
“Then Agrian came along, and they made the change to digital records super easy. They laid out the web interface in a way that was obvious and intuitive,” Rianda said. Integration was the next step. Growers, pest control advisors, agronomists and Morning Star were suddenly all connected into the Agrian system — able to share data seamlessly up and down the supply chain.
Throughout the adoption process, Rianda was in constant contact with the Agrian team. “They are very good about taking suggestions and implementing them quickly if they will benefit most users,” Rianda said. Agrian understands Rianda’s needs because their employees understand the flow from fields all the way to store shelves.
Now, Rianda’s audits take about an hour. She pulls the records electronically, prints recommendations and use reports or sends them electronically. She also completes a daily download from which she checks for potential problems and investigates data if needed.
Morning Star’s return on investment for the Agrian platform was fast. But after Rianda calculated the time and people expenses saved, she said, “We saved what they charge us and then some. I don’t have to hire up to five temporary employees every year. I can keep up with most of it within an hour a day. We also have no manual mistakes because the platform double-checks our work.”
Morning Star’s return on investment for the Agrian platform was fast. But after Rianda calculated the time and people expenses saved, she said, “We saved what they charge us and then some. I don’t have to hire up to five temporary employees every year. I can keep up with most of it within an hour a day. We also have no manual mistakes because the platform double-checks our work.”
“Agrian started in the field first. We tried to build the best possible program based on needs in the field. We developed the largest crop protection label database that is manufacturer indemnified,” said Richard Machado, president of Agrian.
Machado found that it was easy to explain why the switch to their digital platform would benefit processors; crop advisors and growers were already utilizing it, so processors could easily access the information they needed to track and trace crops from seed to store.
Morning Star’s story isn’t unique in the processor world. “Processors want the pesticide use records. We get through these whole end-to-end traceability issues first in the field,” Machado said.
Plus — since every processor experiences audits, whether based on social issues such as sustainability or for food safety reasons, all of them need uniform data. And all of them need a system that is easy to use. “We can automate the process so that processors save time and people, particularly in places where seasonal crops need seasonal workers,” Machado said.
Social media is also forcing the hand of the processing industry.
Years ago, consumers could only find out about outbreaks in a newspaper. Network news sped up the information dissemination, but it wasn’t until recently that social media allowed the instant sharing of news. Now, it is up to a brand to distinguish itself and share their good practices. “You have to show your brand is safe. Shutting down the entire commodity group does significant damage,” Machado said. When suppliers can trace back to the field with the Agrian platform, they can provide the data to absolve a brand of involvement in an outbreak instantaneously.
“We’re seeing an irreversible trend in having more pinpointed data than in the past. Agrian works on both the regulatory and consumer sides. Companies need to be prepared to provide that traceability. It might be data overload, but by filtering the data, it can become useful to a company when they need the data to substantiate their claims about a product,” Machado said.